In today’s fast-paced world, businesses are constantly seeking ways to streamline operations, reduce costs, and improve efficiency. One innovation that’s making a significant impact across industries is the rise of Autonomous Follow Robots (AFRs), particularly in the logistics sector. These smart robots, also known as trackbots, are designed to follow workers and assist with material handling tasks, creating a more efficient and cost-effective environment.
In this blog, we’ll explore how Autonomous Follow Robots are transforming logistics operations, detailing their key advantages and how they contribute to the shift towards automation and smarter logistics management.
What are Autonomous Follow Robots (Trackbots)?
Autonomous Follow Robots are self-driving machines that follow people, objects, or pre-set paths. They are equipped with various sensors and algorithms that allow them to navigate environments, avoid obstacles, and transport goods without the need for human intervention. Trackbots are commonly used in warehouses, factories, distribution centers, and logistics hubs to assist in material handling, reducing the reliance on manual labor while improving productivity.
These robots use cutting-edge technologies such as LiDAR, vision sensors, and machine learning to adapt to their environments, ensuring that they can operate safely and efficiently alongside human workers.
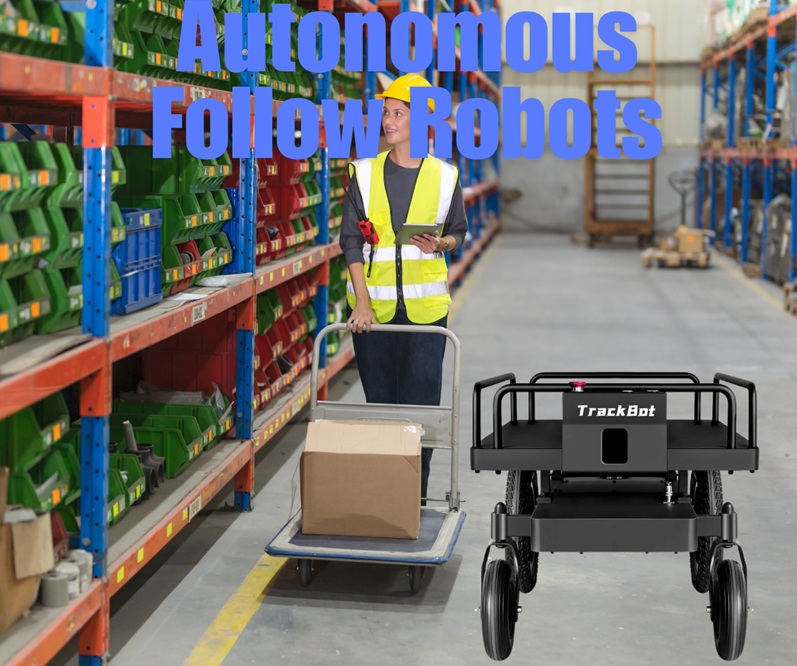
Key Advantages of Autonomous Follow Robots in the Logistics Industry
1. Increased Operational Efficiency
One of the most significant advantages of AFRs in logistics is their ability to boost operational efficiency. In traditional logistics systems, workers often spend valuable time pushing carts, loading and unloading goods, and moving materials from one point to another. These repetitive tasks not only waste time but can also lead to worker fatigue and inefficiency.
Autonomous Follow Robots eliminate the need for workers to manually transport items. By following workers and autonomously transporting goods, AFRs can dramatically reduce the time spent on manual handling tasks, enabling logistics operations to run smoothly and efficiently. Whether it’s moving goods between warehouse aisles or transporting items to shipping zones, trackbots ensure that work flows seamlessly, boosting productivity across the entire supply chain.
2. Cost Reduction in Labor
Labor costs are one of the most significant expenses in the logistics industry. With the rising demand for goods and the pressure to meet fast delivery times, logistics companies are constantly looking for ways to minimize labor costs without sacrificing performance.
Autonomous Follow Robots are a game-changer in this respect. By automating repetitive material-handling tasks, these robots reduce the need for manual labor, leading to significant cost savings in terms of wages and human resource management. Additionally, as trackbots can work 24/7 without needing breaks, companies can achieve greater throughput without having to hire additional staff during peak periods.
3. Improved Accuracy and Safety
Manual handling, while necessary, can be prone to human error. Mistakes such as misplacing goods, damaging products during transport, or even physical injuries from repetitive tasks can be costly for logistics companies. AFRs can help eliminate these risks.
These robots are equipped with advanced sensors and obstacle avoidance systems, allowing them to detect and navigate around obstacles, ensuring safe and accurate deliveries. By avoiding collisions and preventing the mishandling of goods, trackbots help maintain product quality and reduce the risk of accidents in the workplace.
Moreover, AFRs help reduce the physical strain on workers, minimizing the risk of injuries caused by heavy lifting or repetitive movements. This leads to a safer working environment and less reliance on human labor for risky tasks.
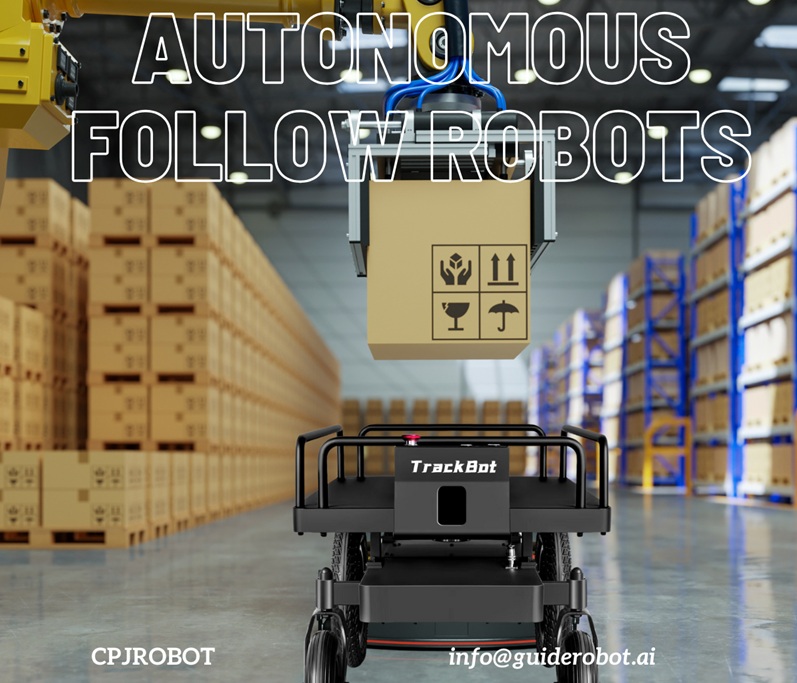
4. 24/7 Operation and Scalability
Unlike human workers, Autonomous Follow Robots are capable of operating around the clock, offering a significant advantage in fast-paced environments. Logistics operations often need to meet tight deadlines and handle large volumes of goods, especially during peak seasons.
AFRs can operate continuously without the need for breaks or shifts, making them ideal for high-demand situations. This continuous operation helps businesses meet peak demands, improve turnaround times, and maintain a high level of service for customers.
Moreover, these robots can easily scale with the growth of your business. As demand increases, more trackbots can be deployed to keep pace with expanding operations, making it easier to scale logistics operations without having to invest heavily in new infrastructure or additional workforce.
5. Seamless System Integration and Flexibility
One of the key strengths of Autonomous Follow Robots is their ability to seamlessly integrate with existing systems. They don’t just work in isolation; they can be connected to other critical systems such as Warehouse Management Systems (WMS), Enterprise Resource Planning (ERP), and Production Control Systems (PCS).
This integration allows AFRs to receive real-time instructions, optimize their paths based on inventory levels, and synchronize with other automated systems within the logistics operation. Additionally, AFRs are flexible enough to adapt to changing environments and workflows, enabling businesses to continuously improve and optimize their logistics processes.
Whether it’s adjusting to changes in warehouse layout, handling a variety of goods, or supporting multiple functions at once, Autonomous Follow Robots provide the flexibility needed to meet the demands of modern logistics operations.
6. Reduced Physical Strain on Workers
Logistics jobs often require workers to lift heavy objects, push carts, and perform repetitive tasks. These physical demands can lead to fatigue, lower job satisfaction, and even injuries over time. Autonomous Follow Robots help solve this problem by taking over many of these labor-intensive tasks.
By automating the transportation of materials, AFRs reduce the physical strain on workers, allowing them to focus on more strategic tasks, such as inventory management, quality control, and customer service. This leads to a happier, healthier workforce and enhances overall workplace productivity.
7. Smart Path Planning and Energy Efficiency
Autonomous Follow Robots are equipped with advanced AI algorithms that allow them to plan the most efficient routes for material handling. By continuously analyzing their environment, AFRs can optimize their paths, reducing unnecessary travel distances and energy consumption.
These smart robots not only increase operational efficiency but also contribute to energy savings and lower operational costs. Whether navigating through large warehouses or adjusting to changes in product locations, AFRs ensure that logistics operations are as efficient and sustainable as possible.
Conclusion: AFRs Are the Future of Logistics
Autonomous Follow Robots are no longer a futuristic concept—they are here, and they’re transforming the logistics industry. With their ability to enhance operational efficiency, reduce labor costs, improve accuracy, and ensure safety, AFRs are playing a critical role in helping logistics companies meet the increasing demands of the modern supply chain.
These robots are enabling businesses to operate more efficiently and cost-effectively, setting the stage for a smarter, more automated logistics ecosystem. As the technology continues to evolve, the impact of Autonomous Follow Robots will only grow, helping businesses stay competitive and meet customer expectations.
Call to Action:
At CPJROBOT, we specialize in the design, manufacturing, and production of LiDAR technology and reception robots, including Autonomous Follow Robots. If you’re looking to optimize your logistics operations with cutting-edge technology, we’re here to help.
Let us show you how our intelligent robots can enhance your productivity and reduce your costs. Contact us today to learn more about our customizable solutions for your logistics needs!